Audits are a key component of maintaining food safety systems and certification to prove to your customers and consumers that the site is following best practices and ensuring production of safe, quality foods. An audit is intended to create transparency in the supply chain, enhance food safety while focusing on continuous improvement. Through the process of program development, implementation, and verification, the preparation for being audited – is no small feat. The team must learn to work in ways that they may not have encountered before such as; documenting actions taken, obtain additional training, and increase the level of communication between departments. Ultimately, the goal is to work in collaboration, follow defined processes and enhance understanding of requirements at all levels. This systematic process, when followed can also help to build a culture of food safety and ensure the team is audit ready every day.
Audits are an important part of the food supply chain?
So it begs the question, if audits are such an important part of the food supply chain…why do we fail or perhaps not do as well as we would hope for you? There may be many factors that contribute such as lack of management commitment, resource challenges, and/or inexperience of the team. Although once we have overcoming some of these earlier hurdles to audit success, we need to shift to thinking more like an auditor and improve our preparation skills. The following Do’s and Don’ts checklist can be one step in understanding what actions you and your team can take or not take before your next audit and why they are important.
Do’s | Don’ts |
---|---|
1. Be Prepared throughout the Year | Wait to the last minute to prepare of the audit |
Why: a site that starts planning in advance will have more time to implement/enhance programs, train the team, and find non-conformances before the audit | |
2. Cross-functional team support and readiness | Have a team of one or just the technical team |
Why: It is impossible to be successful without a team that can help develop, implement, and reinforce policies, procedures, and plans – ensure to involve all key stakeholders and get buy-in along the way. | |
3. Follow your procedures and verify it is working as intended | Let the auditor find issues that the team could of found and addressed proactively |
Why: Verification through inspections and internal audits must be established to ensure the programs put in place are working and if there are non-conforming issues that they are addressed prior to an audit and product is protected. | |
4. Provide Objective Evidence with clear and concise answers to questions | Be Defensive or answer with just closed responses to questions (Yes/No) with no details |
Why: A auditor is required to collect objective evidence through documentation and record review, interviews, and observations. A site that is prepared to provide this information and to give enough details for an auditor to determine conformity will achieve a greater audit success. | |
5. Be Organized | Documents and Records are not readily available and retrieved in a timely manner. |
Why: When the team and the necessary documents are organized, the audit will likely go smoother and provide a way for the auditor to assess the documents and records required to determine conformance. | |
6. Team understands the Code as well as the Auditor | Lack of training of the team and internal audits |
Why: Training is a key component of audit success – not just the main person responsible but all team members – from basic intro food safety to understanding the code requirements which your site will be audited against. Have a team that better understands the ‘what’ and the ‘why’, will help adoption and on-going implementation. | |
7. Develop an Agenda in Collaboration with the auditor | Allowing the auditor to drive the Agenda and all aspects of the audit |
Why: An auditor may have a standard order that they would like to perform the audit but the site must work in collaboration with the auditor to ensure that they understand when shift changes occur, when key stakeholders are available, when certain production or packing is being performed. Providing this knowledge will allow for a more successful flow of the audit and proving compliance. | |
8. Be Positive and be open to the Auditors Findings | Be Combative with the auditor, instead of providing objective evidence to support the rational for why you think it is not a finding |
Why: A positive mindset will calm nerves, provide leadership, and focus not only within the team but also allow the auditor an ability to ask questions and obtain information in a meaningful and open approach. Our goal is to find a balance it taking an audit seriously and understand its a continuous improvement journey. | |
9. Show management commitment and leadership throughout the audit – opening to closing | Having no management representation or engagement throughout the audit |
Why: A management team that is visible throughout the audit as needed and participates in both the opening and closing meetings will provide the auditor an understanding of management commitment. They need to be available to answer questions and to provide supporting evidence when needed (e.g. KPI’s, CAPEX plans, etc.) | |
10. Focus on Continuous Improvement | Have a mindset that creates complacency in programs and attitudes |
Why: The success or failure of audits can hinge on our mindset of continuous improvement – if we are stagnant with our programs, lack change, and poor attitudes this can be our demise but a team that is robust in its change management and plan/do/check/act processes will achieve their goals. |
Tips to Prepare for Your 2022 Food Safety Audit
Audits are a crucial component to maintaining food safety standards and while there is always room continuous improvement within your audit process, there are a number of key components to a successful audit. Proper reporting, active monitoring of critical control points and corrective actions related to food safety plans, food safety systems and auditing, are all essential to effectively communicating throughout your organization – and to meeting food safety requirements.
Watch this on-demand webinar with Denise Webster, Food Safety Expert with QCI Global Assurance to be more prepared for your 2022 audits.
Download Now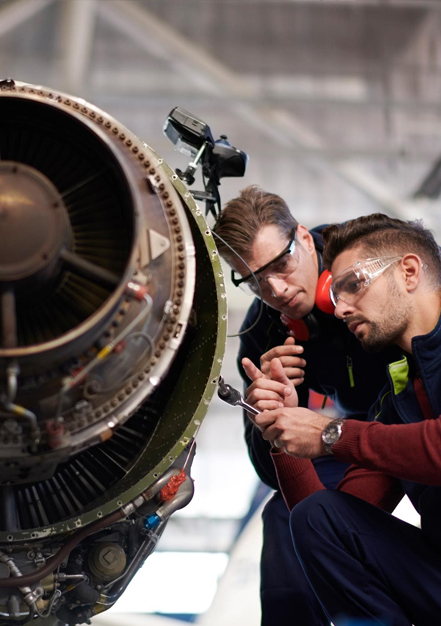
Lastly, the finer points of preparing, navigating, and succeeding during audits will take time and experience. Remember it’s a journey to challenge and grow the site’s food safety program through a commitment of growth, team support, and working to create a stronger food safety culture – to be audit ready, every day!